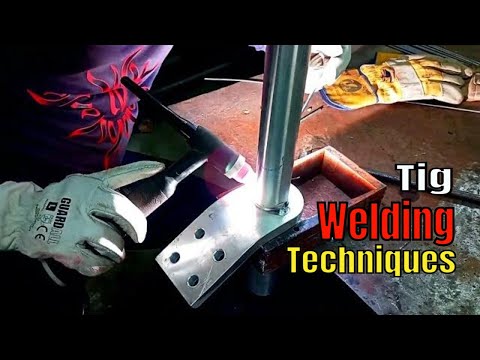
### Metal Fabrication & Welding Overview
Metal Fabrication involves creating metal structures through processes such as cutting, bending, and assembling. It's a critical part of various industries including construction, automotive, aerospace, and manufacturing. Key techniques in metal fabrication include:
1. Cutting: Methods include sawing, shearing, and more advanced techniques like laser cutting, plasma cutting, and water jet cutting.
2. Bending: Achieved through press brakes, tube benders, and rolling machines.
3. Assembling: Involves joining metal parts using methods like welding, riveting, and fastening.
Welding is a primary method used in metal fabrication for joining metals. It involves melting the workpieces and adding a filler material to form a strong joint upon cooling. There are various welding techniques, including:
1. MIG Welding (Metal Inert Gas): Uses a continuous wire feed as an electrode and an inert gas to shield the weld from contamination.
2. TIG Welding (Tungsten Inert Gas): Utilizes a non-consumable tungsten electrode to produce the weld and is known for high-quality welds.
3. Stick Welding (Shielded Metal Arc Welding): Involves a consumable electrode coated in flux to lay the weld.
4. Flux-Cored Arc Welding (FCAW): Similar to MIG welding but uses a special tubular wire filled with flux.
### Steps in Metal Fabrication and Welding Process
1. Design and Blueprint Creation: Engineers create detailed designs and blueprints using CAD (Computer-Aided Design) software.
2. Material Selection: Choosing the appropriate metal based on the requirements of the project, such as strength, weight, and corrosion resistance.
3. Cutting and Shaping: Cutting the metal into required shapes and sizes using various techniques.
4. Forming: Bending and shaping the metal pieces to fit the design specifications.
5. Joining: Welding or otherwise fastening the pieces together.
6. Finishing: Processes such as grinding, polishing, and coating to improve the appearance and durability of the final product.
7. Quality Control: Inspecting the final product to ensure it meets all specifications and standards.
### Applications of Metal Fabrication and Welding
- Construction: Structural beams, columns, trusses, and other components for buildings and infrastructure.
- Automotive: Car bodies, frames, and various mechanical parts.
- Aerospace: Aircraft frames, engine components, and other precision parts.
- Manufacturing: Machinery, tools, and industrial equipment.
- Art and Sculpture: Custom metal artworks and installations.
### Safety in Metal Fabrication and Welding
Safety is paramount in metal fabrication and welding due to the risks associated with high temperatures, electrical equipment, and sharp materials. Key safety measures include:
- Personal Protective Equipment (PPE): Helmets, gloves, aprons, and eye protection.
- Ventilation: Proper ventilation to avoid inhalation of fumes and gases.
- Training: Adequate training for workers on the safe use of tools and machines.
- Regular Maintenance: Ensuring all equipment is regularly inspected and maintained.
### Emerging Trends in Metal Fabrication and Welding
- Automation and Robotics: Increasing use of automated systems and robots for precision and efficiency.
- Advanced Materials: Use of high-strength alloys and composites.
- Sustainable Practices: Emphasis on recycling and environmentally friendly manufacturing processes.
- 3D Metal Printing: Additive manufacturing technologies enabling complex designs and rapid prototyping.
### Conclusion
Metal fabrication and welding are foundational to modern industry, combining traditional craftsmanship with advanced technology to produce essential components across a wide range of sectors. Understanding the various techniques, applications, and safety measures is crucial for anyone involved in this field.
Comments
Post a Comment