Crafting Precision: DIY Lathe Ball Turning Tool for Tie Rod Ball Turning Attachments
Introduction:
In the realm of machining, the ability to craft custom tools is a hallmark of ingenuity and resourcefulness. One such DIY project is the creation of a lathe ball turning tool for tie rod ball turning attachments—a versatile accessory that expands the capabilities of lathe machines. In this article, we explore the process of making a DIY lathe ball turning tool and its application as a tie rod ball turning attachment, offering insights and inspiration for machinists and DIY enthusiasts.
The Need for Custom Tools:
Lathe machines are indispensable in machining operations, offering unparalleled precision and versatility. However, specialized tasks such as turning spherical surfaces, as required for tie rod ball joints, often necessitate custom tools tailored to specific geometries and requirements. Crafting a DIY lathe ball turning tool addresses this need, enabling machinists to produce precise spherical components with ease.
Creating the Lathe Ball Turning Tool:
1. Design and Planning: Begin by conceptualizing the design of the ball turning tool, considering factors such as tool geometry, cutting angles, and materials. CAD (Computer-Aided Design) software can aid in visualizing the tool's components and dimensions before fabrication.
2. Material Selection: Choose high-quality materials suitable for the intended application, such as tool steel or carbide inserts for cutting edges, and aluminum or steel for the tool body. Ensure that the materials are compatible with lathe machining processes and capable of withstanding cutting forces and wear.
3. Machining Process: Utilize lathe machining techniques to fabricate the components of the ball turning tool, including the tool body, cutting insert holder, and adjusting mechanisms. Precision drilling, turning, milling, and grinding may be required to achieve the desired dimensions and tolerances.
4. Assembly and Calibration: Assemble the fabricated components of the ball turning tool, ensuring proper alignment and functionality. Calibration may involve adjusting the cutting insert position, tool angles, and cutting depths to achieve optimal cutting performance and surface finish.
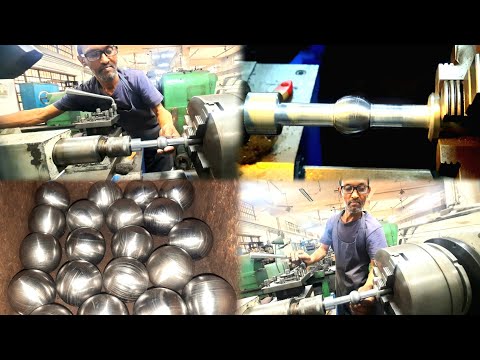
Application as Tie Rod Ball Turning Attachment:
Once the DIY lathe ball turning tool is fabricated and calibrated, it can be mounted on a lathe machine as a tie rod ball turning attachment. This attachment enables machinists to precisely machine spherical surfaces on tie rod ends, steering components, and other automotive or mechanical parts, ensuring proper fit and functionality.
Benefits and Versatility:
The DIY lathe ball turning tool offers numerous benefits and applications, including:
- Customization: Tailoring tool geometry and dimensions to specific machining requirements.
- Cost-effectiveness: Eliminating the need for expensive commercial ball turning attachments.
- Versatility: Adapting the tool for various spherical machining tasks beyond tie rod ball turning, such as knob and handle fabrication, valve seat machining, and model engineering projects.
In the realm of machining, the ability to create perfectly round balls with precision is a hallmark of craftsmanship and technical skill. Whether for decorative purposes, bearing components, or specialized applications, machining round balls on a lathe machine requires meticulous attention to detail and advanced machining techniques. In this article, we explore the process of making round balls on a lathe machine, offering step-by-step guidance and insights for machinists and enthusiasts.
Understanding the Machining Process for Round Balls:
Machining round balls on a lathe machine involves shaping raw material, typically metal, into spherical forms with precise dimensions and surface finishes. This process requires careful planning, tool selection, and machining strategies to achieve the desired results. Here's a detailed overview of the key steps involved:
1. Material Selection: Begin by selecting a suitable material for the round balls, considering factors such as strength, durability, and machinability. Common materials include steel, aluminum, brass, and various alloys.
2. Blank Preparation: Prepare cylindrical blanks of the chosen material, ensuring they are slightly oversized to accommodate machining allowances. The blanks should be centered and securely mounted on the lathe machine's chuck or collet.
3. Tool Selection and Setup: Choose appropriate cutting tools for the machining operation, such as carbide inserts or high-speed steel (HSS) cutting tools with spherical cutting profiles. Install and align the tools on the lathe machine's tool post, ensuring proper clearance and tool angles.
4. Rough Turning: Begin the machining process by rough turning the cylindrical blank to remove excess material and establish a preliminary spherical shape. Use roughing cuts to remove bulk material efficiently while maintaining stability and rigidity.
5. Finish Turning: Once the rough spherical shape is achieved, switch to finer cutting tools and techniques for finish turning. Take light cuts to refine the spherical surface, focusing on achieving precise dimensions and smooth surface finish.
6. Contouring and Polishing: Use contouring tools to refine the spherical shape further and eliminate any irregularities or imperfections. Consider using abrasive polishing compounds or techniques to achieve a mirror-like surface finish on the round balls.
7. Inspection and Quality Assurance: Conduct thorough inspections of the machined round balls using precision measuring tools such as calipers, micrometers, and surface roughness gauges. Verify dimensional accuracy, roundness, and surface finish to ensure compliance with specifications.
8. Finalization and Packaging: Once the round balls pass inspection, finalize the machining process by removing them from the lathe machine and packaging them securely for storage or shipment. Consider applying protective coatings or treatments to enhance durability and prevent corrosion, if necessary.
Conclusion:
Machining round balls on a lathe machine demands precision, expertise, and meticulous attention to detail. By following the outlined steps and employing advanced machining techniques, machinists can produce round balls of exceptional quality and dimensional accuracy, suitable for a wide range of applications in industries such as manufacturing, automotive, aerospace, and beyond. With dedication and craftsmanship, mastering the art of round ball machining opens doors to endless possibilities in precision engineering and manufacturing excellence.
Comments
Post a Comment