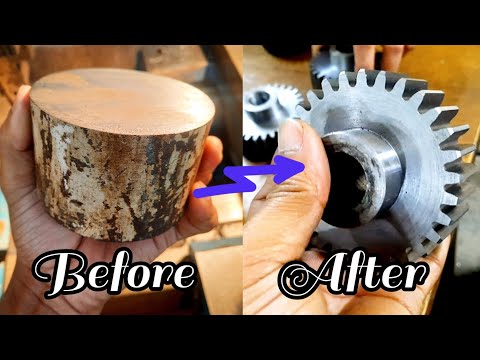
Unveiling the Art of Spur Gear Production: Machining Methods and Techniques
Spur gears are essential components in countless mechanical systems, transmitting motion and power efficiently between shafts. The process of producing spur gears requires precision machining techniques and specialized equipment, with hobbing machines and lathe machines being among the most popular choices. In this article, we delve into the intricacies of spur gear production, exploring the methods, techniques, and machinery involved in creating these fundamental mechanical components.
Understanding Spur Gear Production:
Spur gears are cylindrical gears with teeth that are parallel to the axis of rotation, making them one of the simplest and most commonly used gear types. The production of spur gears typically involves cutting or shaping gear teeth onto a blank workpiece, resulting in a gear that meshes smoothly with other gears to transmit motion and torque.
Key Machining Methods for Spur Gear Production:
1. Hobbing: Hobbing is one of the most widely used methods for producing spur gears, utilizing a hobbing machine to generate gear teeth through a continuous cutting process. The hobbing machine features a hob—a cylindrical cutting tool with helical teeth—that meshes with the rotating workpiece, gradually cutting the gear teeth into the blank as it rotates. This method offers high accuracy, repeatability, and efficiency, making it ideal for large-scale gear production.
2. Milling: Gear milling involves using a milling machine equipped with specialized gear-cutting tools, such as gear cutters or involute gear cutters, to machine gear teeth into a workpiece. This method is versatile and suitable for producing spur gears of various sizes and configurations, albeit with slower production rates compared to hobbing.
3. Shaping: Gear shaping is a machining method that utilizes a shaping machine to cut gear teeth into a blank workpiece using a specially designed cutter. While less common than hobbing or milling, gear shaping can be a cost-effective option for producing spur gears, particularly for smaller production runs or specialized applications.
4. Broaching: Broaching involves using a broaching machine to remove material from a workpiece in a linear motion, typically using a series of teethed cutting edges arranged along a tool called a broach. While primarily used for internal features, broaching can also be adapted for producing external gear teeth, including spur gears, with high precision and efficiency.
Role of Lathe Machines in Gear Production:
While not the primary method for producing spur gears, lathe machines play a significant role in gear manufacturing by providing versatility and flexibility for secondary operations such as turning, facing, and chamfering. Additionally, lathe machines can be used for producing gear blanks or performing finishing operations on gears machined by other methods, enhancing the overall efficiency and quality of the gear manufacturing process.
Spur gear production is a vital aspect of mechanical engineering, with various machining methods and techniques available to meet diverse manufacturing requirements. Whether utilizing hobbing machines, milling machines, shaping machines, or broaching machines, machinists can leverage advanced machining technologies to produce high-quality spur gears that drive innovation and progress in numerous industries. By understanding the capabilities and applications of different machining methods, engineers and manufacturers can optimize spur gear production processes for efficiency, accuracy, and reliability, ensuring the seamless operation of mechanical systems worldwide.
Comments
Post a Comment