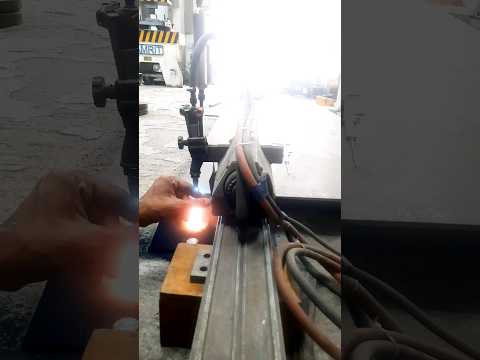
Metal Plate Cutting Fast and Accurately with the Gas Cutting Torch | Oxygen & Acetylene Fuel!
Mastering Metal Plate Cutting with Precision: The Gas Cutting Torch Technique
Introduction:
Metal plate cutting is a fundamental process in various industries, ranging from manufacturing to construction. When it comes to cutting thick metal plates swiftly and accurately, the gas cutting torch emerges as a time-tested solution. Utilizing a blend of oxygen and acetylene fuel, this technique offers both speed and precision, making it indispensable for many fabrication tasks.
In this article, we delve into the intricacies of metal plate cutting with a gas cutting torch, exploring its principles, advantages, and best practices.
Understanding the Gas Cutting Torch:
The gas cutting torch operates on the principle of oxy-fuel combustion, where a mixture of oxygen and acetylene is ignited to produce an intensely hot flame. This flame, directed onto the metal surface, rapidly heats the material to its kindling temperature. Simultaneously, a jet of pure oxygen is blown onto the heated metal, causing it to oxidize and form metal oxide. The exothermic reaction between the oxygen and the metal sustains the cutting process, resulting in a clean, precise cut.
Advantages of Gas Cutting Torch Technique:
1. Versatility: Gas cutting torches can effectively cut through a wide range of metals, including steel, stainless steel, aluminum, and copper, making them suitable for diverse applications.
2. Speed: Compared to traditional methods like sawing or grinding, gas cutting torches offer significantly faster cutting speeds, enabling swift completion of fabrication tasks.
3. Precision: With proper technique and equipment, gas cutting torches can achieve high levels of precision, producing clean cuts with minimal distortion.
4. Cost-Effectiveness: Despite the initial investment in equipment and gases, the overall cost of gas cutting is relatively low, especially for large-scale cutting operations.
Best Practices for Gas Cutting Torch Operation:
1. Equipment Inspection: Before commencing any cutting operation, thoroughly inspect the gas cutting torch, hoses, regulators, and other components for signs of damage or wear. Replace any faulty parts to ensure safe and efficient operation.
2. Proper Setup: Position the workpiece securely on a stable surface, ensuring adequate clearance for the torch movement. Adjust the gas pressures and torch angle according to the material thickness and cutting speed requirements.
3. Preheating: Start by preheating the metal surface with the outer flame of the torch. Move the torch smoothly along the intended cutting line to achieve uniform heating.
4. Cutting Technique: Once the metal reaches the kindling temperature, introduce the oxygen jet to initiate the cutting process. Maintain a steady torch speed and angle to control the cutting depth and achieve a smooth, clean cut.
5. Post-Cutting Inspection: After completing the cut, inspect the edges for any signs of slag or irregularities. Use appropriate tools to remove any excess material and achieve the desired finish.
Conclusion:
The gas cutting torch technique remains a cornerstone of metal fabrication due to its combination of speed, versatility, and precision. By understanding the principles of oxy-fuel combustion and following best practices for operation, fabricators can harness the full potential of this cutting method to achieve superior results in various industrial applications.
Comments
Post a Comment