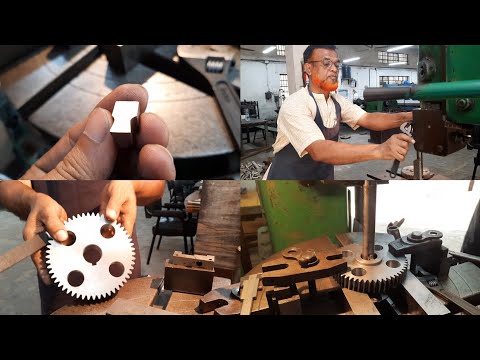
Machining a Replacement Gear Keyway: How to Make a Keyway on a Slotting Machine
Introduction:
Replacing a gear in machinery often requires precision machining to ensure proper fit and functionality. One crucial aspect of this process is creating a keyway, a slot in the shaft that allows the gear to be securely mounted and transmit torque effectively. In this article, we'll explore the process of machining a replacement gear keyway using a slotting machine, detailing the steps involved and highlighting the importance of accuracy and attention to detail.
Understanding Keyways and Their Importance:
Keyways are slots cut into shafts and hubs of gears and other rotating components to provide a secure connection and prevent slippage. They allow for the transmission of torque between the shaft and the mounted component, ensuring smooth and efficient operation of the machinery. Machining a precise keyway is essential to maintain proper alignment and prevent premature wear and damage to the gears and other components.
The Role of Slotting Machines:
Slotting machines, also known as slotter machines, are precision machining tools used to create slots, keyways, and other intricate features in metal workpieces. They consist of a vertical ram with a cutting tool that moves vertically to cut into the workpiece mounted on a rotary table. Slotting machines are widely used in manufacturing and repair operations, particularly in industries such as automotive, aerospace, and machinery.
Step-by-Step Guide to Making a Keyway on a Slotting Machine:
1. Preparation: Begin by securing the workpiece, typically the shaft containing the gear, on the rotary table of the slotting machine. Ensure that the workpiece is securely clamped to prevent movement during machining.
2. Selection of Cutting Tool: Choose a cutting tool appropriate for the size and depth of the keyway required. The cutting tool should have sharp edges and be capable of cutting through the material of the workpiece efficiently.
3. Setting Cutting Parameters: Adjust the speed and feed rate of the slotting machine according to the material of the workpiece and the specifications of the keyway. Proper cutting parameters are essential to achieve accurate and consistent results.
4. Machining the Keyway: Lower the vertical ram of the slotting machine and engage the cutting tool with the surface of the workpiece. Begin the cutting process by moving the ram vertically while simultaneously rotating the rotary table to create the desired shape and depth of the keyway.
5. Continuous Monitoring: Throughout the machining process, monitor the cutting operation closely to ensure that the keyway is being formed accurately and to detect any signs of tool wear or deviation from the intended dimensions.
6. Final Inspection: Once the keyway has been machined to the required specifications, inspect it carefully to verify its dimensions, surface finish, and alignment with the gear and shaft. Make any necessary adjustments or corrections to achieve the desired fit and functionality.
Conclusion:
Machining a replacement gear keyway on a slotting machine requires precision, skill, and attention to detail. By following the steps outlined in this article and employing proper cutting techniques, machinists can create keyways that meet the exact specifications of the gear and shaft, ensuring reliable performance and longevity of the machinery. Whether in manufacturing or repair operations, slotting machines play a crucial role in producing accurate and durable keyways essential for the smooth operation of various mechanical systems.
Comments
Post a Comment